新聞資訊
News information
聯(lián)系我們
Contact us
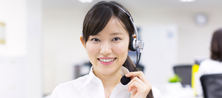
營銷中心(國內):0760-23210602
海外事業(yè)部(國外):+86-13928213830
營銷顧問:0760-23210603 國內郵箱: sales10@kisense.com
國際郵箱: postmaster@kisense.com
網(wǎng)址:nhyrrnw.cn
地址:中山市東鳳鎮(zhèn)同樂工業(yè)園玉峰路28號
新聞詳情
干貨 | 一文看懂數(shù)控四軸加工中心應該如何對刀 | ||||
發(fā)布者:admin | 添加時間:2019/12/10 | 瀏覽次數(shù):1806 | ||
一、刀位點 刀位點是刀具上的一個基準點,刀位點相對運動的軌道即加工道路,也稱編程軌道。 二、對刀和對刀點 對刀是指數(shù)控操作員在啟動數(shù)控程序之前,通過必定的丈量手段,使刀位點與對刀點重合。可以用對刀儀對刀,其操作比較簡略,丈量數(shù)據(jù)也比較精確。還可以在數(shù)控機床上定位好夾具和安裝好零件之后,運用量塊、塞尺、千分表等,運用數(shù)控機床上的坐標對刀。關于操作者來說,判定對刀點將是非常重要的,會直接影響零件的加工精度和程序控制的精確性。在批出產(chǎn)進程中,更要考慮到對刀點的重復精度,操作者有必要加深對數(shù)控設備的了解,掌握更多的對刀技巧。
(1)對刀點的選擇準則 在機床上簡略找正,在加工中便于檢查,編程時便于核算,并且對刀過失小。 對刀點可以選擇零件上的某個點(如零件的定位孔中心),也可以選擇零件外的某一點(如夾具或機床上的某一點),但有必要與零件的定位基準有必定的坐標聯(lián)絡。 前進對刀的精確性和精度,即使零件要求精度不高或許程序要求不嚴厲,所選對刀部位的加工精度也應高于其他方位的加工精度。 選擇接觸面大、簡略監(jiān)測、加工進程安穩(wěn)的部位作為對刀點。 對刀點盡或許與規(guī)劃基準或工藝基準一致,避免由于標準換算導致對刀精度甚 至加工精度下降,增加數(shù)控程序或零件數(shù)控加工的難度。 為了前進零件的加工精度,對刀點應盡量選在零件的規(guī)劃基準或工藝基準上。例如以孔定位的零件,以孔的中心作為對刀點較為適宜。 對刀點的精度既取決于數(shù)控設備的精度,也取決于零件加工的要求,人工檢查對刀精度以前進零件數(shù)控加工的質量。尤其在批出產(chǎn)中要考慮到對刀點的重復精度,該精度可用對刀點相對機床原點的坐標值來進行校核。 (2)對刀點的選擇方法 關于數(shù)控車床或車銑加工中心類數(shù)控設備,由于中心方位(X0,Y0,A0)已有數(shù)控設備判定,判定軸向方位即可判定整個加工坐標系。因此,只需求判定軸向(Z0或相對方位)的某個端面作為對刀點即可。 關于三坐標數(shù)控銑床或三坐標加工中心,相對數(shù)控車床或車銑加工中心凌亂很多,根據(jù)數(shù)控程序的要求,不只需求判定坐標系的原點方位(X0,Y0,Z0),并且要同加工坐標系G54、G55、G56、G57等的判定有關,有時也取決于操作者的習氣。對刀點可以設在被加工零件上,也可以設在夾具上,可是有必要與零件的定位基準有必定的坐標聯(lián)絡,Z方向可以簡略的通過判定一個簡略檢測的平面判定,而X、Y方向判定需求根據(jù)具體零件選擇與定位基準有關的平面、圓。 關于四軸或五軸數(shù)控設備,增加了第4、第5個旋轉軸,同三坐標數(shù)控設備選擇對刀點類似,由于設備愈加凌亂,一同數(shù)控系統(tǒng)智能化,供給了更多的對刀方法,需求根據(jù)具體數(shù)控設備和具體加工零件判定對刀點相對機床坐標系的坐標聯(lián)絡可以簡略地設定為互相關聯(lián),如對刀點的坐標為(X0,Y0,Z0),同加工坐標系的聯(lián)絡可以定義為(X0+Xr,Y0+Yr,Z0+Zr),加工坐標系G54、G55、G56、G57等,只需通過控制面板或其他方法輸入即可。這種方法非?;罱j,技巧性很強,為后續(xù)數(shù)控加工帶來很大便利。 一旦由于編程參數(shù)輸入差錯,機床發(fā)生磕碰,對機床精度的影響是喪命的。所以關于高精度數(shù)控車床來說,磕碰事端要根絕。 (3)磕碰發(fā)生的最主要的原因: a.對刀具的直徑和長度輸入差錯; b.對工件的標準和其他相關的幾許標準輸入差錯以及工件的初始方位定位差錯; c.機床的工件坐標系設置差錯,或許機床零點在加工進程中被重置,而發(fā)生改動,機床磕碰大多發(fā)生在機床快速移動進程中,這時分發(fā)生的磕碰的損害也最大,應肯定避免。 所以操作者要特別注意機床在履行程序的初始階段和機床在替換刀具的時分,此刻一旦程序修改差錯,刀具的直徑和長度輸入差錯,那么就很簡略發(fā)生磕碰。 在程序結束階段,數(shù)控軸的退刀動作順序差錯,那么也或許發(fā)生磕碰。
|